Among Vögele’s highlights at bauma 2025 were its first fully-electric compact paver, the Super 1300-5e, as well as its Mini 500e and Mini 502e electric pavers. All three models feature a battery-electric drive concept and an electrically heated extending screed. As low-noise machines with zero operating emissions, they are ideal for paving in urban settings, in enclosed spaces, or in particularly sensitive areas.
The Super 1300-5e is not only the first fully-electric Compact Class paver from Vögele, but also the first electric paver of the Dash 5 generation. In combination with the AB 340 extending screed, the machine offers pave widths of between 1.8 m and 4.2 m, making it an excellent choice for small and medium-scale road construction projects. The liquid-cooled Li-ion battery from Kreisel Electric has a storage capacity of 126 kWh and works with 400 V in the high-voltage range. Depending on the paving method, it provides sufficient reserves of power for a full working day.
With its high-performance battery, the Super 1300-5e achieves comparable drive power and paving performance to its conventionally powered counterparts in the Compact Class. As a Dash 5 paver, it also provides an even higher level of operating comfort, automated functions and shorter set-up times than its Dash 3 predecessor. The new technologies include the ErgoPlus 5 operating concept, new assistance and automatic control systems, additional comfort features and a new lighting system.
The Mini 500e and Mini 502e battery-electric Mini Class pavers will be available from June 2025 with a choice of two battery options: the standard option has a storage capacity of 15 kWh and delivers sufficient power for a full working day. For longer operating times, Vögele offers an alternative 22 kWh battery option, which is good for up to two days of paving without recharging. Both battery options work in the low voltage range with 48 V. In combination with the electrically heated AB 135 extending screed, these mini pavers have pave widths from 0.25 to 1.8 m.
Both the electric Mini Class pavers and the Super 1300-5e can be charged quickly and easily. The mini pavers can be connected to a household socket or a wallbox. Depending on the battery version, the charging process takes around five to seven hours, the easiest way being to connect the Super 1300-5e to a wallbox or a charging station. With a charging capacity of 22 kW, charging takes around five hours, while connecting to a rapid charging station can shorten this to just one hour. As the compact pavers utilise the same battery and drive technologies as all other compact e-machines from the Wirtgen Group, users also enjoy the added value of synergy effects resulting from common charging procedures, maintenance & service and spare and wear parts.
Hamm electric rollers
Furthermore, Hamm has introduced its fully-electric roller, the HX 70e VV-S, equipped with two vibration drums. This model will also be joined by the HX 70e VO-S, a sales variant with an oscillation drum. As an ongoing technology project, these tandem rollers are initially being put into operation on inner-city construction sites in Europe.
The Hamm HX 70e is powered by a 400-V Li-ion battery from Kreisel with a capacity of 63 kWh. The machine is charged via a Type 2 connector, with other charging options such as Type 1, J1772 and CCS also to be added. With the fast charge option, the battery can be charged from 20% to 80% in under an hour.
Owing to the electrical components, the battery-powered tandem rollers are not only quieter but also more efficient in operation than their diesel-driven counterparts. This is especially true for the models with the oscillation drum. Here, the already low noise of oscillation is combined with the quiet electric drive, making the machines suitable for use in vibration-sensitive and noise-sensitive environments, such as within the vicinity of hospitals or historical buildings.
The HX 70e tandem rollers deliver the same compaction power as the diesel-engine machines and in fact produce a higher output at their peak. The electric rollers are operated in virtually the exact same way as the conventional diesel counterparts, with the only difference being the display, which now features new symbols to give operators an intuitive user experience.
Another benefit of the battery-powered tandem rollers is their lower maintenance requirement. With the electrical components of the high-voltage system having long maintenance intervals and not being subject to the same maintenance requirements specific to diesel engines, users can benefit from low operating costs. What’s more, just like the diesel-powered machines, the new electric models can also be connected to the John Deere Operations Centre.
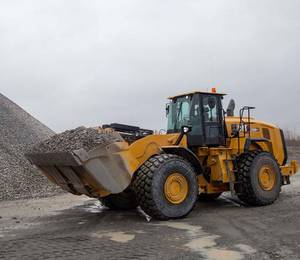

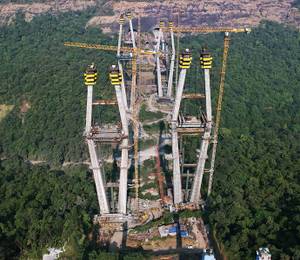
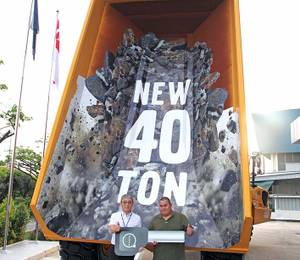
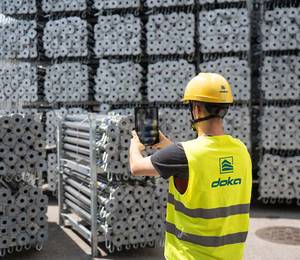
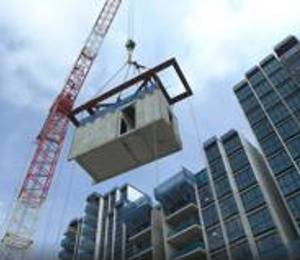
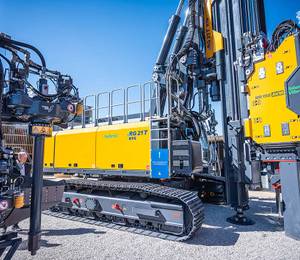
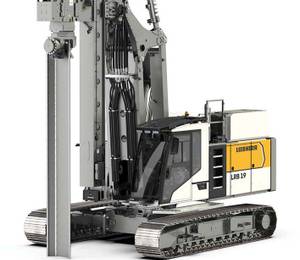